
Plenary Talks
Project Professor Kouhei Ohnishi
Haptics Research Center, Keio University
KISTEC
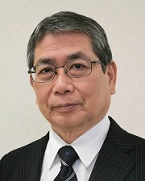
Abstract: A bottleneck of automation is found at atypical task in manufacturing process. The much effort to introduce the industrial robot into such process has been made for long time. These challenges were more or less replacing the human skills with the AI-based and/or sensor-based motion by the industrial robot. Some experiments were successful however the flexibility needed in atypical tasks is not always obtained.
The brain part for the industrial robot has been strengthened by the network and the AI. The motion of the industrial robot has been extended by both more DoFs and sensor-based planning of motion. These developments would bring the dexterous motion of the industrial robot. But the reality is far from the expectation. There is still a missing link remained. This issue prevents the industrial robot from getting the flexibility like human even if the intelligent functions are installed.
The missing link must be a tie between the brain and the body however this link has been a mystery. The human neuron connects these two and that is indispensable for the contact task in atypical process. The similar function is necessary in the robot. Recently it is clarified that the real haptics can work similarly just as human neuron in motion process. That makes the robot more flexible and adaptive. The bilateral function of the real haptics brings the complete recording of motion data. Since the motion data includes the human skill, it will be used in the atypical task by the robot.
The talk will show how the robot can acquire the human skill through the real haptics technology, and how the skill of the human can be reproduced in the robot. The real haptics and the AI technology will change the robot smarter one.
Biography: Professor Kouhei Ohnishi has been with Keio University since 1980, and is Professor Emeritus and Project Professor at the Haptics Research Center. He was serving as President of the IEEE IES in 2008-2009 and President of the IEE of Japan in 2015-2016. He received the prestigious awards including the IEEE IES Dr.-Ing. Eugene Mittelmann Achievement Award (2004), Fukuzawa Award (2014), Medal with Purple Ribbon from His Majesty the Emperor (2016) and so on. He authored and co-authored many books and papers including “Motion Control Systems” (Wiley/IEEE Press 2011), and “Mechatronics and Robotics” (CRCPress2020). His research interest includes motion control, haptics, mechatronics, power electronics and so on.
Professor Masayoshi Tomizuka
Cheryl and John Neerhout, Jr. Distinguished Professor
Director, Mechanical Systems Control (MSC) Laboratory
Department of Mechanical Engineering
University of California, Berkeley
Berkeley, California 94720, U.S.A.
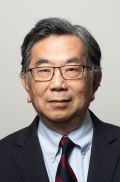
Abstract: Intelligent decision making and control enhances the performance of industrial robots performing tasks such as object handling, assembly, trajectory following and interaction with human workers and other robots. High level decision making includes strategy development and planning. The low level decision making is made by the robot controller to perform hybrid position/force control, impedance control, motion control and so on. In this talk, I will review several projects conducted at the Mechanical Systems Control (MSC) laboratory of the University of California, Berkeley on the development of intelligent strategies and controls for robots. They include 1. online gain optimization for variable impedance control, 2. Learning from demonstration for robotic assembly tasks, and 3. manipulation of deformable objects and 4. Human-robot collaboration. Motivation, approach, simulation and experimentation will be presented for each of these projects.
Biography: Dr. Masayoshi Tomizuka received his B.S. and M.S. degrees in Mechanical
Engineering from Keio University, Japan and his Ph. D. degree from the
Massachusetts Institute of Technology in February 1974. In 1974, he joined
the faculty of the Department of Mechanical Engineering at the University
of California at Berkeley, where he currently holds the Cheryl and John
Neerhout, Jr., Distinguished Professorship Chair. His current research
includes optimal and adaptive control, digital control, motion control,
and applications to robotics and manufacturing, vehicles and mechatronic
systems. He served as Program Director of the Dynamic Systems and Control
Program of the National Science Foundation (2002-2004). He has supervised
about 130 Ph. D. students to completion.He served as President of the American
Automatic Control Council (AACC) (1998-99). He chaired the IFAC Technical
Committee on Mechatronic Systems. He is Honorary Member of the ASME, Life
Fellow of IEEE, and Fellow of the International Federation of Automatic
Control (IFAC). He is the recipient of the J-DSMC (Journal of Dynamic Systems,
Measurement and Control) Best Paper Award (1995, 2010), the Charles Russ
Richards Memorial Award (ASME, 1997), the Rufus Oldenburger Medal (ASME,
2002), the John R. Ragazzini Award (AACC, 2006), the Richard Bellman Control
Heritage Award (AACC, 2018), the Honda Medal (ASME, 2019) and the Nichols
Medal (IFAC, 2020).
Dr. Koji Yasui
Chief Technical Supervisor
Industrial Mechatronics Division
FA Systems Group
MITSUBISHI ELECTRIC Corporation
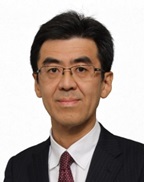
Abstract: The manufacturing industry has been adopting automated production lines by using digital technologies since early stage, and very recently the trials are going to be accelerated by using state-of-the-art technologies such as AI and 5G/6G influenced by the COVID-19 pandemic.
the movement has been recognized as IoT and/or DX.
Since the target market is related to the so-called sustainable society, the progress is remarkable not only in speed but also in scale. The application of quantum technology in response to this major movement has also emerged. In this talk, I will introduce the
preparatory activities for this major trend, the recent situation, and the outlook for the next
20~30 years.
Biography: Dr. Yasui is a senior chief technologist at the Factory Automation Systems Group of Mitsubishi Electric Corporation. Dr. Yasui is also a sub-program director of a SIP program supported by the government and an invited professor at Osaka University. He has worked as a product development researcher, research manager, a visiting researcher at Stanford University, a labor union branch executive committee chairman, a manufacturing manager, a company-wide development strategy manager at the head office, and a laboratory manager. He is is currently providing solutions to global customers. He received his B.S. degree (1982) and Ph.D. degree (1989) from the University of Tokyo. Contact information: Yasui.Koji@aj.MitsubishiElectric.co.jp, LinkedIn
Professor Jianjun Shi
The Carolyn J. Stewart Chair and Professor
A Member of the National Academy of Engineering of USA
Georgia Institute of Technology
jianjun.shi@isye.gatech.edu
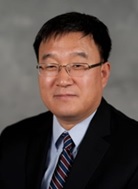
Abstract:This presentation introduces the concepts of In-Process Quality Improvement (IPQI) in smart manufacturing systems, with a focus on the need to enhance machine automation to serve IPQI purposes. Conventional machine automation adjusts a system's inputs to achieve high precision of the outputs, typically reaching and maintaining the setting points of position, speed, temperature, force, torque. Unlike the conventional automation, the IPQI enhanced automation instead adjusts the system’s inputs to achieve the optimal quality of the product by closing the loop and making full use of in situ quality sensing signals for feedback or feed-forward control. Due to the new product quality focused control objective, IPQI enhanced automation has several unique characteristics in terms of its treatments of in situ quality measurement signals, sampling frequencies, system dynamics, which raise significant challenges in system modeling and control methodology development. This talk will provide a systematic analysis contrasting IPQI enhanced automation with conventional machine automation. Several new methodologies and applications of IPQI enhanced automation will be discussed.
Biography: Dr. Jianjun Shi is the Carolyn J. Stewart Chair and Professor in the
School of Industrial and Systems Engineering, with a joint appointment
in the School of Mechanical Engineering, both at Georgia Institute of Technology.
Prior to joining Georgia Tech in 2008, he was the G. Lawton and Louise
G. Johnson Professor of Engineering at the University of Michigan. He received
his B.S. and M.S. in Electrical Engineering from Beijing Institute of Technology
in 1984 and 1987, and his Ph.D. in Mechanical Engineering from the University
of Michigan in 1992.
Dr. Shi’s research focuses on data enabled manufacturing, and system informatics and control. His methodologies integrate system informatics, advanced statistics, and control theory, and fuse engineering system models with data science methods for design and operational improvements of manufacturing systems. The technologies developed by Dr. Shi’s research group have been implemented in a wide variety of production systems and produced significant economic impacts.